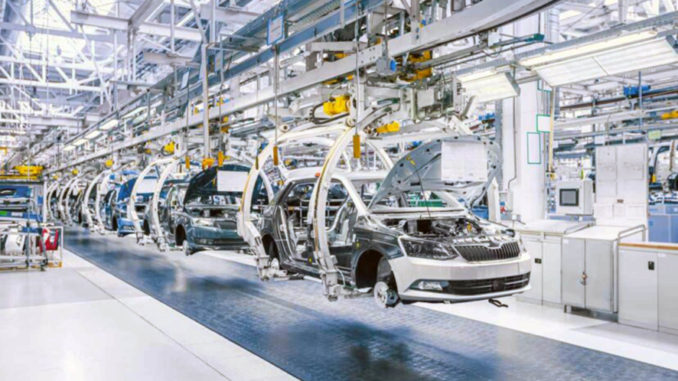
La cadena de montaje lineal que Ford aplicó al fabricar vehículos representó en 1908 el inicio de la revolución productiva en serie, redujo costos y precios finales, minimizó procesos, masificó productos, expandió el mercado y el consumo y crecieron los salarios a diferencia del Taylorismo que contando con la división del trabajo especializado y conocimiento técnico del obrero; se tradujo en permanentes huelgas por la caída salarial al imponerse controles de tiempos y movimientos para reducir costos buscando incrementar la acumulación del capital.
La estrategia de ampliación productiva vía máxima estandarización e inclusión de la faja transportadora en las plantas de Ford creó un sistema continuo automatizado en el ensamblaje vehicular permitiendo que los obreros no tuvieran que ir detrás de cada unidad para montarlos porque al sustituir el prototipo sólido y compacto existente, hacia otro por partes; la industria automotriz dio el salto revolucionario que varios sectores productivos copiaron hasta su reemplazo por el toyotismo en la década del 70.
Previo al proceso evolutivo fordista, en 1901 Ransom Eli Olds desarrolló la cadena de montaje estacionaria y con esta el Oldsmobile Curved Dash, considerado el primer vehículo fabricado en masa. Olds siguió el concepto de la organización científica del trabajo planteada por Taylor fabricando 19.000 vehículos que contrasta con el novedoso proceso fabril fordista que permitió manufacturar más de 15 millones de modelos T gracias a una permanente reducción de precios, al cambio de horas de montaje automotor de 12,5 horas a 93 minutos, a la subida del salario a cinco dólares la hora por ocho horas diarias laboradas cuando en esa época los salarios fueron inferiores trabajando inclusive más tiempo por día generando la creación de otro turno determinante para que la producción aumentara en 50% más.
La crisis petrolera de 1973 devino en la caída del fordismo y dio pase al Justo a tiempo aplicado por Toyota, técnica consistente en lograr mayor eficiencia en la cadena de suministros siendo necesario exacta retroalimentación entre proveedores, productores y operadores logísticos para evitar retrasos.
Este modelo abandonó la producción en serie y almacenaje fordista y se enfocó en producir bajo demanda de manera que, al eliminar inventarios; la reducción de costos logísticos llevó a ofrecer menores precios. Bajo el criterio cero errores, cero averías, cero demoras, cero papel y cero existencias, surge la estrategia “cinco ceros” que al planear eficacia al 100% involucra a los trabajadores para crear valor hacia el cliente final.
La reciente innovación de ensamblaje que promueve Tesla denominada “Unboxed” llevará a eliminar todo el recorrido de la cadena de montaje y conducirá a lograr 50% de ahorro en la fabricación que potenciarán la comercialización masiva futura de vehículos eléctricos .
Los espero en el siguiente artículo
Juan Távara Balladares
CEO y fundador
www.carrosok.com
Autoridad automotriz